Your Trusted Sydney Flower Delivery Service!
We believe every flower tells a story. Whether it’s to say “Thank You,” celebrate love, or brighten someone’s day, our handpicked, beautifully arranged flowers are perfect for any occasion.
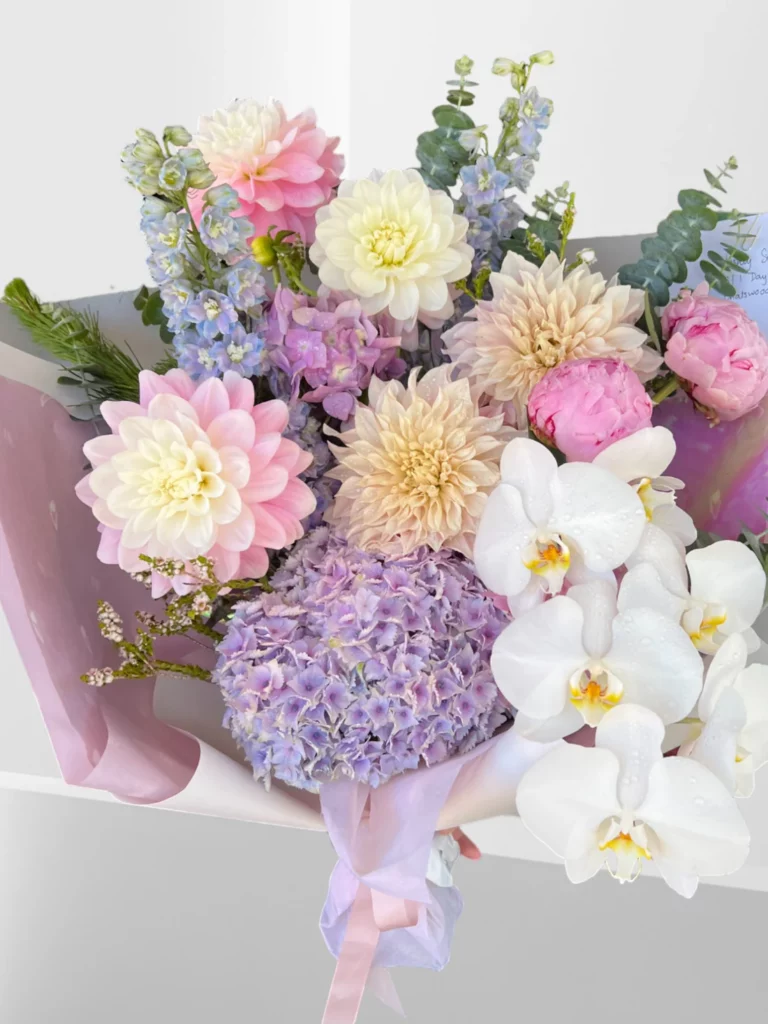
About Us
Welcome to Bio Ponica, your trusted destination for stunning floral arrangements and reliable flower delivery in Sydney. At Bio Ponica, we believe in the power of flowers to express emotions, celebrate milestones, and brighten lives. With our passion for blooms and commitment to excellence, we’ve become a go-to choice for all your floral needs.
Our Services
1.Thank You Flowers
Show your appreciation with elegant bouquets designed to express heartfelt gratitude. Our thank-you flowers convey emotions perfectly, leaving a lasting impression on your loved ones.
2. Sydney Flower Delivery
Fresh flowers, delivered right to your doorstep anywhere in Sydney. We guarantee prompt and reliable delivery so your flowers arrive in perfect condition every time.
3.Wedding Flowers
Make your big day unforgettable with our bespoke wedding flower arrangements. From bridal bouquets to centerpieces, we bring your dream wedding to life with floral artistry.
4. Mother’s Day Flowers
Celebrate the queen of your life with beautiful blooms that say “thank you” and “I love you.” Our Mother’s Day arrangements are as unique and special as she is.
5.Birthday Flowers
Surprise your loved ones with vibrant birthday bouquets! Choose from cheerful, colorful arrangements that add joy and beauty to their special day.
6. Next-Day Flower Delivery
Need flowers fast? We’ve got you covered. With our next-day delivery service, you’ll never miss an important occasion, no matter how last-minute it is.
Why Choose Us?
- Freshness Guaranteed: We source the finest flowers to ensure your arrangements stay fresh and vibrant.
- Same & Next-Day Delivery: Fast and dependable delivery for your convenience.
- Customizable Bouquets: Tailor your order to fit any occasion, style, or message.
- Sustainably Sourced: We care about the planet and use eco-friendly practices in every arrangement.
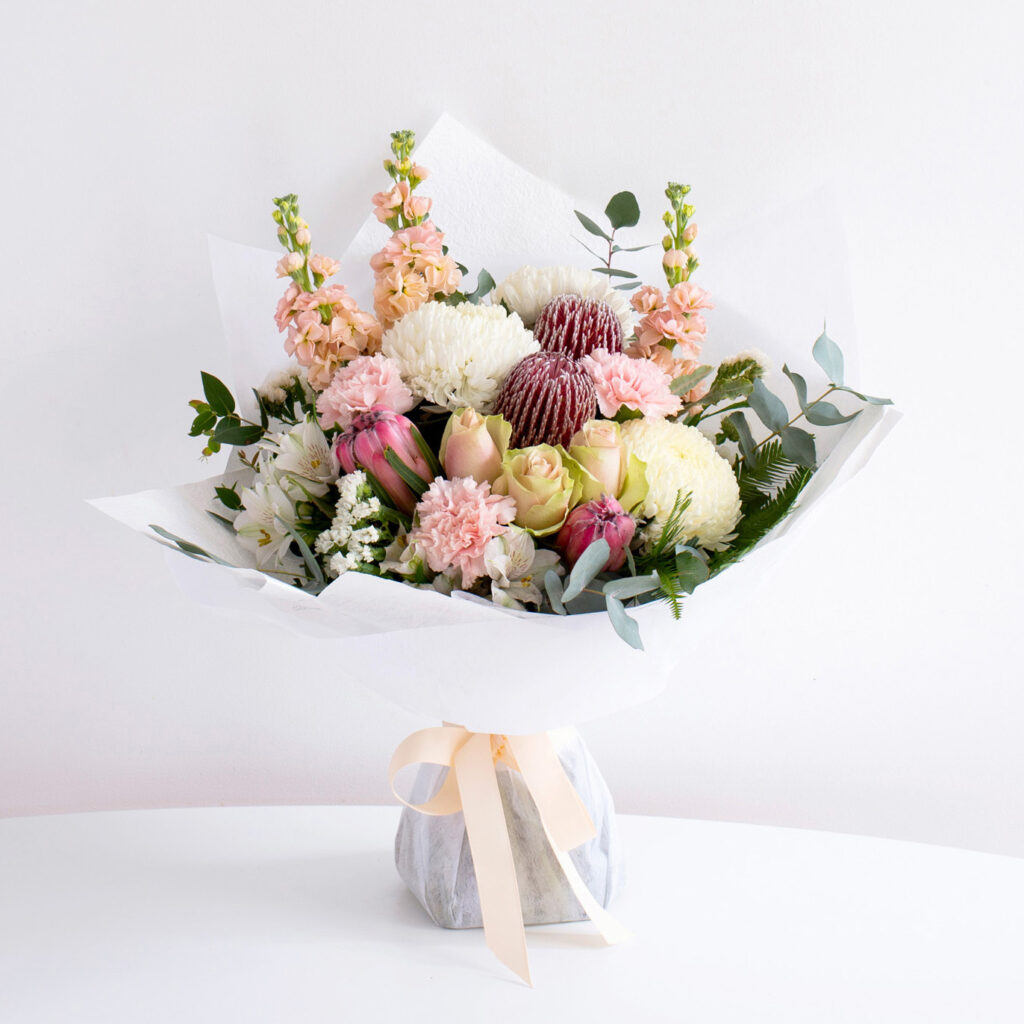
Post
Hear What Our Customers Say
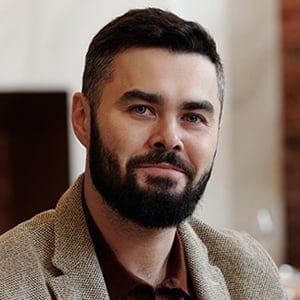
James Sikes
"I ordered a bouquet for my mom on Mother’s Day, and it was beyond beautiful. The flowers were fresh, vibrant, and delivered right on time. Thank you, Bio Ponica, for making her day so special!"
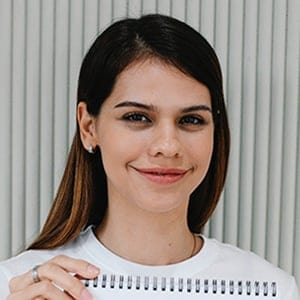
Angela Higgins
"I’ve used Bio Ponica multiple times for birthdays and anniversaries, and they never disappoint. Their arrangements are always exquisite, and the delivery is super reliable. Highly recommend!"
Popular Questions
What areas do you deliver to?
We deliver across Sydney and surrounding suburbs. Whether it’s for a home, office, or event venue, we ensure your flowers arrive fresh and on time.
Can I get same-day delivery?
Yes! We offer same-day delivery for orders placed before [insert time, e.g., 2:00 PM]. Orders placed after this time will be scheduled for next-day delivery.
Do you offer next-day flower delivery?
Absolutely! Our next-day delivery service is perfect for last-minute surprises or planning ahead.
Can I customize my bouquet?
Yes, we provide custom floral arrangements tailored to your preferences. Let us know your color palette, flower choices, or special requests, and we’ll create something unique for you.
How do I place an order?
Placing an order is easy! Simply browse our collection online, select your desired bouquet, and proceed to checkout. Alternatively, you can call us for personalized assistance.